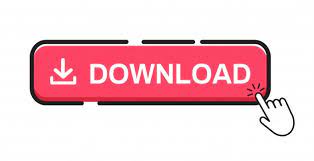
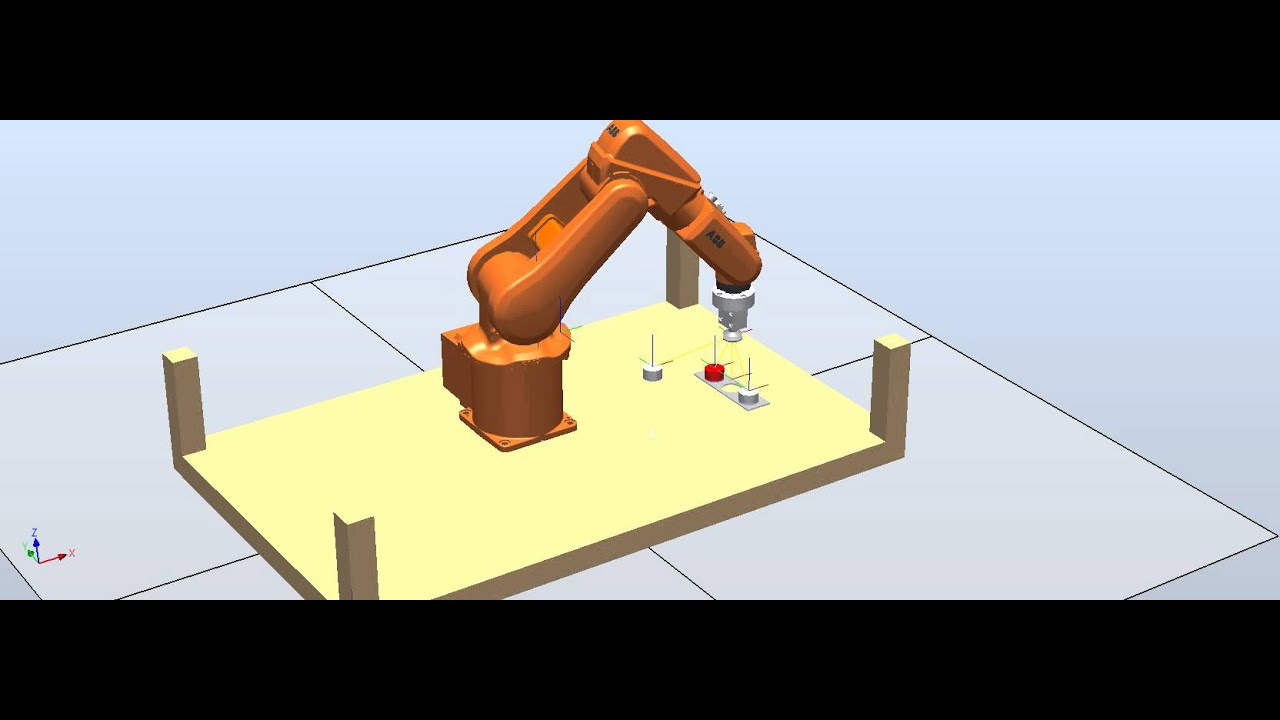
After 18 months HPM had saved enough on scrap and labor to invest in its first new robot. Over the next year HPM added five more used S3 robots, applying what they learned from the initial system to automate other compact presses.
#ABB ROBOTSTUDIO T GRIPPER MANUAL#
The new system allowed HPM to move several of the manual machine handlers to less mundane positions in the plant, reducing the stress of a repetitive task and reallocating the labor in a more efficient manner. Properly programmed and outfitted, robots are much more gentile at handling the parts,” said Adams.
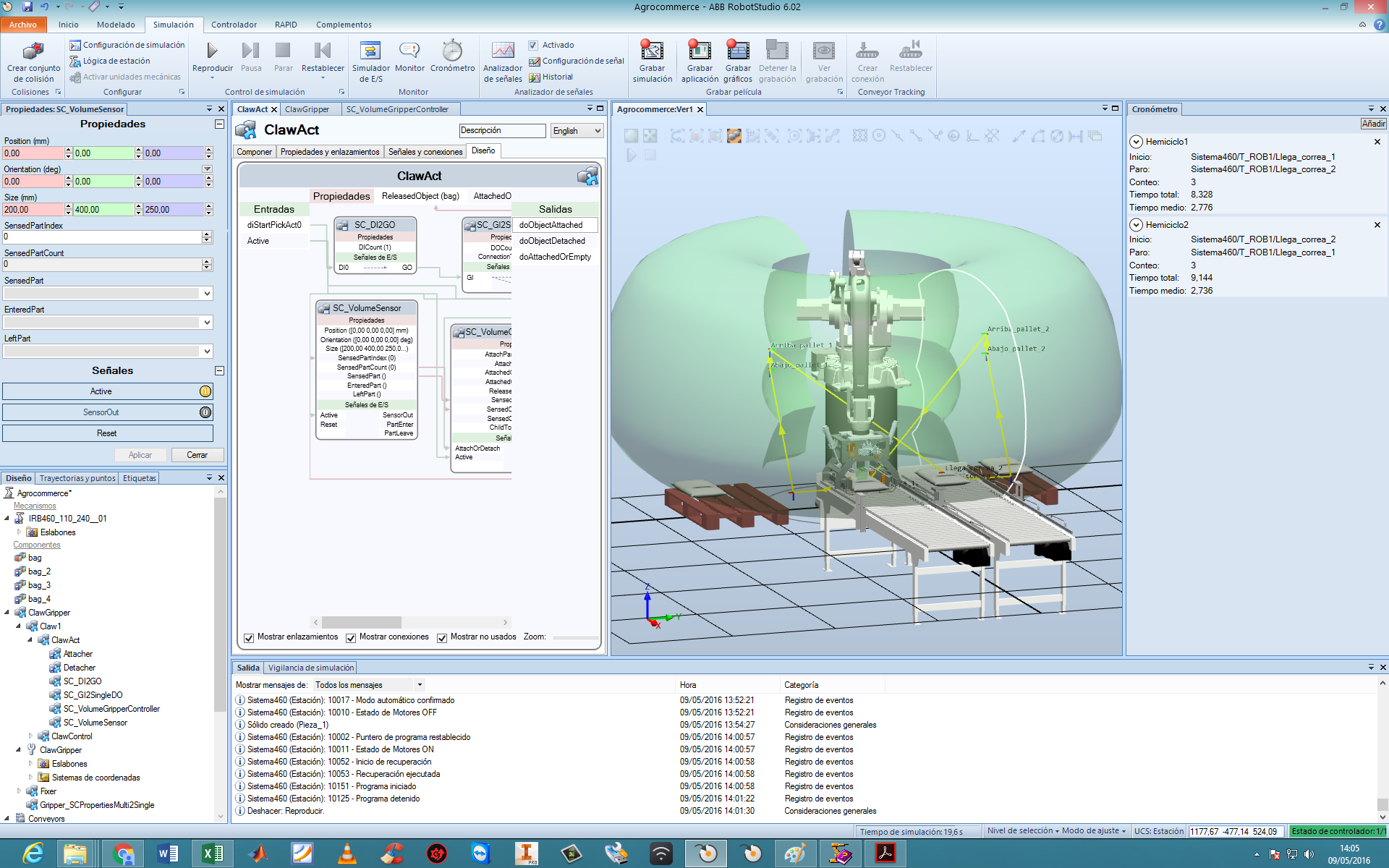
The part could be imperceptibly deformed, but you wouldn’t know it until it came out of the oven five hours later. “When the parts were manually being pulled out of the press there was considerable handling damage. With the newly installed robot, featuring an electric magnetic gripper to handle the part, the scrap rate of the new product went from 11% while manually tended to 0.5%. When the powdered metal parts come out of the press, before they are hardened in the oven, they can easily crumble with even the lightest touch. “They also provided us some much-needed support with programming and integrating the system into the existing operation.” Reduced scrap, more efficient labor allocation “CIM had a used robot that would allow us to ease our way into robotic automation, limiting our initial exposure just in case it didn’t perform as intended,” said Adams. system integrator) in the US, from his work with robots at his previous employer. James Adams, who had joined HPM several years earlier as a manufacturing development engineer, was familiar with CIM, the longest-tenured ABB Robotics Value Provider (i.e.
#ABB ROBOTSTUDIO T GRIPPER TRIAL#
In an effort to keep costs down and to minimize any exposure during the initial trial period, HPM purchased a used, vintage 1993, ABB S3 robot from CIM SYSYEMS INC. “Reducing labor costs was also a factor, but shortly after the first installation a major automotive OEM opened a manufacturing facility in town, and our labor cost issue transitioned to a labor availability issue, as it became extremely difficult to hire and retain employees.” “We started with robots because we had a part to make for a customer that had small, very fragile teeth that couldn’t be handled manually, and at that point all of our compacting presses were tended by hand,” said Gregory Owens, president of the HPM Greensburg plant. HPM began a gradual investment in industrial robots in 2005, driven by the emergence of a tightening labor market and the opportunity to produce an extremely fragile product. It specializes in producing valve train and transmission components for automotive tier suppliers in the United States, with a growing presence serving motorcycle and landscape equipment manufacturers. The Hitachi Powdered Metals (HPM) plant in Greensburg, Indiana is one of nine such Hitachi facilities worldwide.
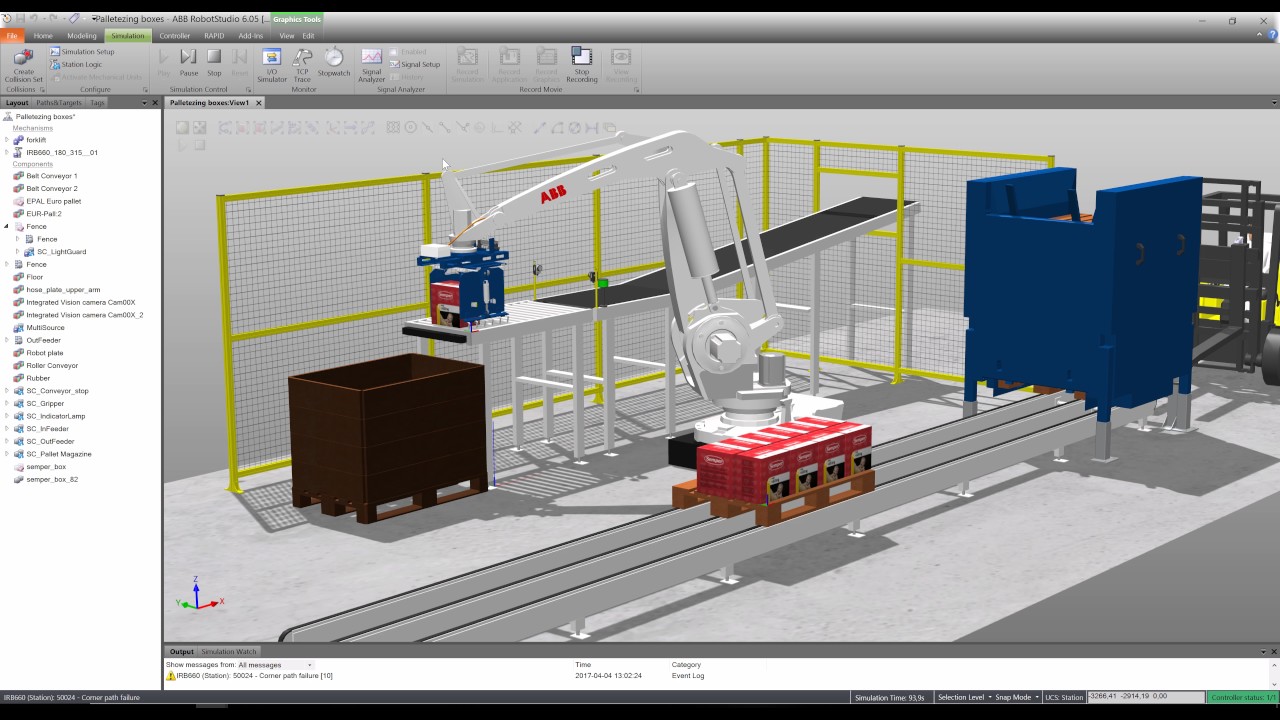
Custom powder alloy mixtures provide the ability to produce complex, even intricate parts that meet the strength and tolerance specifications required for highly demanding applications. Once compacted, the shapes are heated in a controlled atmosphere furnace to bond the particles and harden the parts.Īlso known as green compacting, the process yields near-net components that typically use more than 97% of the initial raw material in the finished part. Powdered Metallurgy (PM) or sintering is the process of compacting custom blends of elemental or alloy powders in prefabricated dies to efficiently make machine parts of varying complexity. With its electric magnetic gripper the robot was able to handle the parts more gentle than the most cautious employee, reducing the scrap rate of the new product from 11% to 0.5%.Today HPM started with a handling application to tend the fragile parts. Fast forward to today, over 200 robots working at HPM’s Greensburg plant. HPM started with a pre-used robot to get familiar with robots and gain experience. The solution to solve both issues at the same time was robot automation. And secondly, the customer demand to produce extremely small and fragile parts which were barely handable by hand. It was very difficult to hire and retain skilled employees. Back in 2005 Hitachi Powered Metals faced two challenges at the same time.
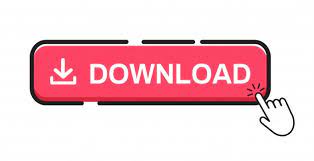